What is Dispenser Pump?
A dispenser pump is a mechanical or electromechanical device designed to accurately measure and release a specific quantity of a substance—typically liquid, gel, or foam—from a container. Unlike simple caps or open-mouth bottles, dispenser pumps provide controlled delivery, minimizing waste and ensuring consistency. They are commonly found in consumer goods, healthcare products, and industrial settings, where precision and hygiene are paramount.
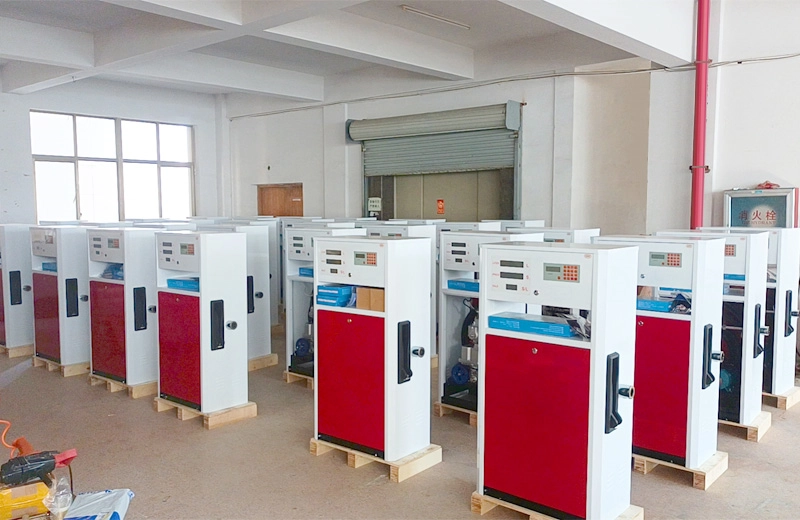
At its core, a dispenser pump consists of a few key components:
- Actuator: The button or lever pressed by the user to initiate dispensing.
- Piston or Plunger: A moving part that creates pressure to push the product out.
- Chamber: A reservoir that holds the product before dispensing.
- Valves: Check valves (inlet and outlet) that regulate the flow direction.
- Dip Tube: A tube that draws the product from the container into the pump mechanism.
How Does a Dispenser Pump Work?
The operation of a dispenser pump relies on basic principles of fluid dynamics and mechanical pressure. Here’s a step-by-step breakdown of its working mechanism:
Priming: When the pump is first used, the user presses the actuator, creating a vacuum in the chamber. This vacuum pulls the product up through the dip tube and into the chamber via the inlet valve.
Compression: Upon releasing the actuator, a spring returns the piston to its original position. This compresses the product in the chamber, closing the inlet valve and forcing the substance through the outlet valve.
Dispensing: The product exits through the actuator nozzle, delivering a pre-measured dose. The outlet valve closes again to prevent air or contaminants from entering the system.
Recovery: The pump resets, ready for the next use. Most pumps are self-priming, meaning they retain enough product in the chamber for immediate dispensing in subsequent uses.
This cycle ensures consistent, controlled dispensing with minimal user effort.
Types of Dispenser Pumps
Dispenser pumps vary in design based on their intended use, viscosity of the product, and operational environment. Common types include:
Manual Dispenser Pumps
- Lotion Pumps: Designed for thick liquids like creams or shampoos, these pumps often have wide nozzles and require moderate pressure to dispense.
- Foam Pumps: These mix air with the liquid to create foam, commonly used for hand soaps.
- Trigger Sprayers: Utilize a trigger mechanism for spraying liquids (e.g., cleaning products).
Airless Dispenser Pumps
- Ideal for oxygen-sensitive products like serums or pharmaceuticals. They use a vacuum-sealed system where a piston moves upward as the product is dispensed, preventing air from entering the container.
Electric Dispenser Pumps
- Battery-operated or plug-in pumps that automate dispensing. Often used in soap dispensers in public restrooms or for medical fluids.
Industrial Dispenser Pumps
- Heavy-duty pumps designed for high-viscosity substances (e.g., adhesives, lubricants) or hazardous chemicals. These may include peristaltic or diaphragm pumps for precise control.
Applications of Dispenser Pumps
The versatility of dispenser pumps makes them indispensable across industries:
Consumer Goods
- Personal care: Shampoos, conditioners, lotions, and hand sanitizers.
- Household products: Dish soaps, detergents, and surface cleaners.
Healthcare
- Precise dosing of medications, such as eye drops or liquid antibiotics.
- Alcohol-based sanitizers in hospitals to ensure hygiene.
Food and Beverage
- Dispensing condiments (ketchup, mustard), cooking oils, or syrups in commercial kitchens.
Industrial and Automotive
- Lubricants, adhesives, and solvents in manufacturing processes.
Cosmetics
- High-end serums and foundations where precise application matters.
Advantages of Dispenser Pumps
- Controlled Dosage: Eliminates guesswork and reduces product waste.
- Hygiene: Minimizes contamination by limiting contact with the product.
- User Convenience: Effortless operation with one-handed use.
- Versatility: Adaptable to various viscosities and container sizes.
Challenges and Considerations
While dispenser pumps offer numerous benefits, they are not without limitations. Thick or abrasive substances may clog the mechanism, requiring frequent maintenance. Additionally, complex designs can increase production costs. Manufacturers must balance functionality with affordability and sustainability, as plastic pumps contribute to environmental waste. Recent innovations include biodegradable materials and refillable systems to address these concerns.
Maintenance and Troubleshooting
Proper care ensures longevity:
- Clean nozzles regularly to prevent clogs.
- Avoid exposing pumps to extreme temperatures.
- For airless pumps, replace the container once empty, as they cannot be refilled.
The Future of Dispenser Pumps
As technology evolves, dispenser pumps are becoming smarter. Sensor-activated pumps in touchless dispensers, common in public restrooms, reduce cross-contamination risks. IoT-enabled pumps in industrial settings can monitor usage and automate refills. Sustainability trends are also driving the adoption of recyclable materials and refill stations.
Conclusion
The dispenser pump is a marvel of engineering that blends simplicity with functionality. From ensuring hygiene in hospitals to delivering the perfect dose of luxury skincare, these devices have revolutionized how we interact with everyday products. As innovation continues, dispenser pumps will likely become even more efficient, eco-friendly, and integral to both consumer and industrial ecosystems. Understanding their mechanics and applications not only highlights their importance but also underscores the role of thoughtful design in enhancing modern life.
Understanding the Dispenser Pump: Function, Design, and Applications
A dispenser pump is a ubiquitous yet often overlooked mechanical device designed to control the flow of liquid or semi-liquid substances from a container. Found in everyday products ranging from hand soap bottles to pharmaceutical serums, dispenser pumps combine practicality, precision, and user convenience. This article explores the mechanics, components, applications, and advantages of dispenser pumps, shedding light on their critical role in modern packaging solutions.
What Is a Dispenser Pump?
A dispenser pump is a manually operated mechanism that enables users to dispense a measured amount of product with minimal effort. Unlike aerosol sprays or open-cap containers, dispenser pumps rely on mechanical action—typically a spring-loaded system—to draw liquid from a reservoir and release it through a nozzle. The design ensures controlled dosing, reduces waste, and maintains product hygiene by minimizing contact with air or contaminants.
Key Components of a Dispenser Pump
The functionality of a dispenser pump depends on its carefully engineered components:
Actuator (Nozzle): The topmost part pressed by the user. Its shape determines the flow pattern—such as a stream, mist, or foam—and often includes a locking feature to prevent accidental discharge during transport.
Piston Chamber: A cylindrical housing containing a piston that moves up and down to create suction. When the actuator is pressed, the piston compresses, forcing liquid upward; releasing it creates a vacuum to draw more liquid into the chamber.
Dip Tube: A long, narrow tube extending from the pump into the product. It channels liquid upward from the bottom of the container to the piston chamber.
Spring: Located inside the piston chamber, the spring returns the actuator to its original position after each use, resetting the pump for the next dose.
Valves: Check valves (often ball-shaped) regulate unidirectional flow. An inlet valve prevents backflow into the container, while an outlet valve ensures liquid exits only through the nozzle.
Housing/Collar: The outer structure that secures the pump to the container, usually via screw threads or a snap-fit design. Tamper-evident seals are common in pharmaceutical or cosmetic products.
How Does a Dispenser Pump Work?
When a user presses the actuator, the piston compresses the spring, increasing pressure in the chamber. This forces the outlet valve open, expelling the liquid through the nozzle. Releasing the actuator allows the spring to decompress, creating a vacuum that closes the outlet valve and opens the inlet valve. New liquid is drawn into the chamber via the dip tube, ready for the next cycle. Each press delivers a consistent volume, typically ranging from 0.25 mL to 5 mL, depending on the pump’s design.
Applications Across Industries
Dispenser pumps are integral to numerous sectors due to their versatility and reliability:
Personal Care & Cosmetics: Hand soaps, lotions, shampoos, and serums rely on pumps for hygienic, mess-free application. Foam pumps aerate liquids into a rich lather, while fine-mist sprays are used for toners or perfumes.
Pharmaceuticals: Dose-controlled pumps ensure accurate delivery of medications like eye drops, nasal sprays, or topical creams. Child-resistant designs enhance safety.
Food & Beverage: Dispensers for cooking oils, condiments, or syrups prioritize ease of use and portion control. High-viscosity pumps handle products like honey or peanut butter.
Household & Industrial Cleaners: Detergents, disinfectants, and solvents use rugged pumps resistant to harsh chemicals. Trigger sprays are common for surface cleaners.
Automotive & Lubricants: Grease and oil dispensers feature durable materials to withstand high-pressure environments.
Advantages of Dispenser Pumps
- Precision: Ensures consistent dosing, critical for medications or premium cosmetics.
- Hygiene: Reduces contamination risks by avoiding direct contact with the product.
- Cost-Efficiency: Minimizes product waste compared to open jars or pour spouts.
- User Experience: Ergonomic designs cater to single-handed operation and accessibility.
- Versatility: Adaptable to liquids of varying viscosities, from water-thin to gel-like.
Design Considerations
Manufacturers tailor dispenser pumps to specific needs:
- Material Compatibility: Pumps are made from plastics (e.g., polypropylene), glass, or metals, chosen for chemical resistance and durability.
- Viscosity Range: Thicker liquids require pumps with wider valves and stronger springs.
- Anti-Clog Features: Nozzles with self-cleaning mechanisms prevent blockages in products prone to drying.
- Sustainability: Eco-friendly pumps use recyclable materials or incorporate refillable systems to reduce plastic waste.
Limitations and Innovations
While dispenser pumps excel in many areas, challenges include potential leakage under extreme temperatures or pressure. Innovations like airless pumps (which use a vacuum to dispense 100% of the product) and smart pumps with digital dose counters are addressing these issues. Biodegradable materials and “green chemistry” designs are also gaining traction.
Conclusion
The dispenser pump is a marvel of functional design, blending mechanical simplicity with user-centric innovation. From safeguarding health through precise drug delivery to enhancing daily routines with elegant cosmetic packaging, these devices exemplify how small engineering solutions can have an outsized impact on convenience and sustainability. As technology evolves, dispenser pumps will continue to adapt, meeting the demands of both consumers and industries in an increasingly eco-conscious world.
What is a Dispenser Pump? A Comprehensive Overview
In today’s world, where efficiency, precision, and hygiene are paramount, dispenser pumps have become indispensable tools across various industries. From medical facilities to food service and personal care, these devices play a critical role in ensuring the accurate and controlled distribution of liquids, gels, and other substances. But what exactly is a dispenser pump, and how does it function? This article explores the definition, mechanisms, applications, and significance of dispenser pumps in modern society.
Definition and Basic Functionality
A dispenser pump is a mechanical or electronic device designed to dispense measured amounts of a substance, typically a liquid or semi-liquid, from a container. Unlike traditional open containers or simple pour spouts, dispenser pumps offer controlled, hygienic, and consistent dosing. They are commonly used in scenarios where precision, safety, and ease of use are essential.
The core principle of a dispenser pump revolves around pressure regulation and flow control. By applying force—whether manually, pneumatically, or electrically—the pump draws the substance from its reservoir and releases it in a predetermined quantity. This mechanism ensures that users receive the exact amount needed without waste or contamination.
Types of Dispenser Pumps
Dispenser pumps come in various designs, each tailored to specific applications:
Manual Dispenser Pumps:
These are the most common and straightforward type. Operated by hand, they rely on a user pressing a lever or button to activate the pumping mechanism. For example, a manual pump on a hand sanitizer bottle uses a spring-loaded system to release a fixed volume of gel with each press.
Pneumatic Dispenser Pumps:
These pumps use compressed air to generate the force required for dispensing. They are widely used in industrial settings where high precision and automation are necessary, such as in pharmaceutical manufacturing or chemical processing.
Electric Dispenser Pumps:
Powered by batteries or electricity, these pumps offer advanced features like programmable dosing, digital controls, and integration with smart systems. They are popular in healthcare (e.g., IV fluid delivery) and commercial kitchens for automated liquid dispensing.
Gravity-Based Dispenser Pumps:
Some designs utilize gravity to facilitate the flow of liquids, often combined with a valve system to regulate the output. These are commonly found in household products like dish soap dispensers.
Each type has its advantages, depending on factors like cost, required accuracy, and environmental conditions.
Key Components and Working Mechanism
A typical dispenser pump consists of several key components:
- Reservoir: The container holding the substance to be dispensed.
- Pump Body: The housing that contains the internal mechanisms.
- Valve System: Regulates the flow of the substance, ensuring it is released only when activated.
- Actuator: The part the user interacts with (e.g., a button or lever) to trigger the dispensing process.
- Nozzle or Spout: Directs the substance to the desired location.
When the actuator is pressed, the pump creates a vacuum or pressure differential that draws the substance from the reservoir through the valve and out of the nozzle. The design of the valve and the pump’s internal geometry determine the volume dispensed per cycle. For instance, a 10 mL pump will release exactly 10 milliliters with each activation, minimizing waste and ensuring consistency.
Applications Across Industries
Dispenser pumps are versatile tools with applications spanning multiple sectors:
Healthcare:
In hospitals and clinics, dispenser pumps are used for administering medications, disinfectants, and intravenous fluids. They reduce the risk of cross-contamination and ensure precise dosing, which is critical for patient safety.
Personal Care and Cosmetics:
Products like hand sanitizers, lotions, and facial cleansers often feature dispenser pumps to provide hygienic and measured application. This is especially important in public spaces such as schools, offices, and airports.
Food and Beverage Industry:
Dispenser pumps are used to portion out ingredients like syrups, oils, and sauces in restaurants and food processing plants. They help maintain consistency in recipes and reduce labor costs.
Industrial and Manufacturing:
In sectors like automotive, construction, and electronics, dispenser pumps apply adhesives, lubricants, and sealants with high precision, improving product quality and efficiency.
Household and Consumer Goods:
From laundry detergents to cooking oils, dispenser pumps enhance convenience and reduce spillage, making them a staple in modern homes.
Advantages of Dispenser Pumps
The widespread adoption of dispenser pumps can be attributed to their numerous benefits:
- Hygiene: Minimizes direct contact with the substance, reducing the risk of contamination.
- Accuracy: Ensures consistent dosing, which is vital in medical and industrial contexts.
- Efficiency: Saves time and resources by eliminating the need for manual measurement.
- Safety: Prevents overuse or misuse of potentially hazardous substances.
- Sustainability: Reduces waste by delivering precise amounts, promoting resource conservation.
Challenges and Considerations
While dispenser pumps offer significant advantages, they also present challenges. For example, improper maintenance can lead to clogging or malfunction, particularly with viscous substances. Additionally, the initial cost of high-precision models may be prohibitive for some users. However, advancements in materials and design continue to address these issues, making dispenser pumps more reliable and affordable.
Conclusion
A dispenser pump is far more than a simple tool for pouring liquids—it is a sophisticated device that combines engineering ingenuity with practical utility. Whether in a hospital, a kitchen, or an industrial plant, these pumps enhance efficiency, safety, and precision. As technology evolves, we can expect even more innovative designs that cater to diverse needs, further solidifying the dispenser pump’s role as a cornerstone of modern life. Understanding their functionality and applications not only highlights their importance but also empowers users to make informed choices in their respective fields.